Bridging the gap between the physical and digital requires fast, accurate data.
Introducing the Siemens Success Story: A Proven Approach to Seamless Enterprise Integration and Observability Solutions. Through our collaboration with Siemens Digital Industries, a global leader in technology and engineering, we achieved remarkable results by leveraging modern integration techniques
A division of Siemens AG, Siemens DI is a market leader in industrial automation and industrial software. Its solutions power a lot of what makes our day-to-day lives possible. The cars that we drive, the food that shows up on our dinner tables, the medicine we pick up from our local pharmacy, the washing machines we use to do laundry, the phones in our pockets — chances are, these were either manufactured or developed using software and solutions from Siemens DI. More than 170,000 customers use its software to make data-driven decisions and help them make sense of massive amounts of industrial IoT data.
Siemens DI adopted Splunk and Rojo’s Splunk apps to monitor its data streaming ecosystem and the KPIs associated with it: IT-relevant KPIs that track the amount of data consumed by its line of business, the intervals of data consumption, and the health and performance of the platform overall. Its teams also used Splunk to monitor business relevant KPIs to support sales offices worldwide. Adopting Splunk was pivotal for Siemens DI, as it helped them understand the data streams and start their observability journey.
75+ countries and 120+ SAP systems
Improved data transparency for customers across 75+ countries and 120+ SAP systems.
10 million product and pricing items
Reduced time to synchronize for 10 million product and pricing items from weeks to real-time
Greater product reliability and customer satisfaction
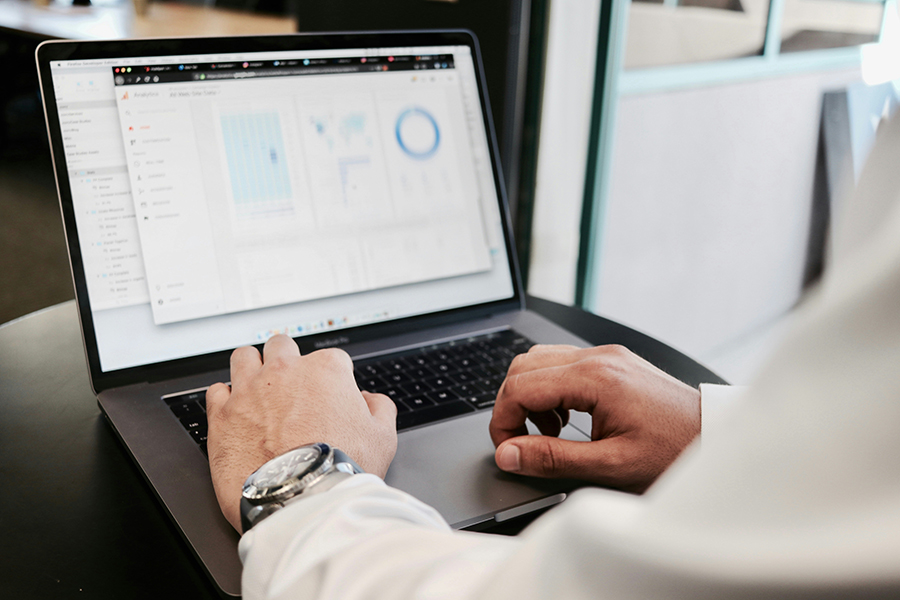
Key challenges
Siemens Digital Industries experienced data latency and limited visibility across its complex and large system landscape, due to the increasing amount of data exchanged across applications and business processes. This resulted in a negative impact on business users related to SAP product master data synchronization.
Key outcomes
After introducing a new integration strategy with Splunk Cloud as its observability platform and Rojo Consultancy’s Splunk Apps for Confluent Kafka and SnapLogic, Siemens DI significantly reduced data latency. It also reduced operating costs significantly, increased efficiency and scalability, and improved customer satisfaction.
“The transparency we never had”
With Siemens DI’s data streaming services for product information — called Product Master Data Streaming (PMDS) — customers can process and consume data to feed other systems. Siemens DI uses SnapLogic to integrate data from multiple sources into data streams, which are powered by Confluent Kafka. However, Siemens DI was missing insight into what was happening in those data streams. Errors in data could originate in SAP systems — or from suppliers that customers had integrated — and negatively affect performance. Since customers didn’t have access to the data that would help them resolve issues, Siemens DI had to field service calls to troubleshoot on their behalf.
“Initially we used Splunk Enterprise to monitor our integration pipelines and event-driven platform,” says Afonso Rodrigues, citizen integrator on PMDS at Siemens DI. “We log about two dozen fields of metadata that we can then analyze and build our dashboards on. Splunk gives us the transparency we never had.” Employing Splunk was made simple, because Rojo Consultancy offered Splunk observability apps to integrate the Splunk platform with SnapLogic, as well as Kafka. This integration means Siemens DI’s teams can monitor various applications in Siemens DI’s ecosystem using a single view.
Speedy resolution for performance issues
Companies using export, transform, load (ETL) tools to automate data processing rely on their data streams to be accurate and timely. But for Siemens the large volume of data from many sources presented more opportunity for errors to disrupt the process. “The main issues were that ETL-based processes can have huge amounts of data that need to be replicated and transformed multiple times in order to arrive and be useful to our customers,” says Thomas Hecht, IT project lead and corporate process owner for product master data at Siemens DI. “If errors come through, it can be difficult to know where they’re coming from, which app, which data source. Splunk gives everyone, the customer and us, the ability to quickly find the problem and speed resolution.”
Siemens DI also uses the insight within the Splunk platform to monitor performance. It often identifies issues before customers do and can proactively alert users and provide the necessary information to resolve issues. Siemens DI monitors service level agreement (SLA) performance for all connected systems to maintain compliance.
"Addressing Siemens DI's critical pain points – data latency and limited visibility during data-synchronisation integration errors – was our top priority. Leveraging our expertise in Event-Driven Architecture and Observability. This led to significant improvements in data-latency, cost efficiency, scalability, and customer satisfaction. Looking ahead, we're excited to enhance Siemens DI's solution with actionable insights for both business and IT."
Shashank Singh, Senior Integration Architect at Rojo Integrations
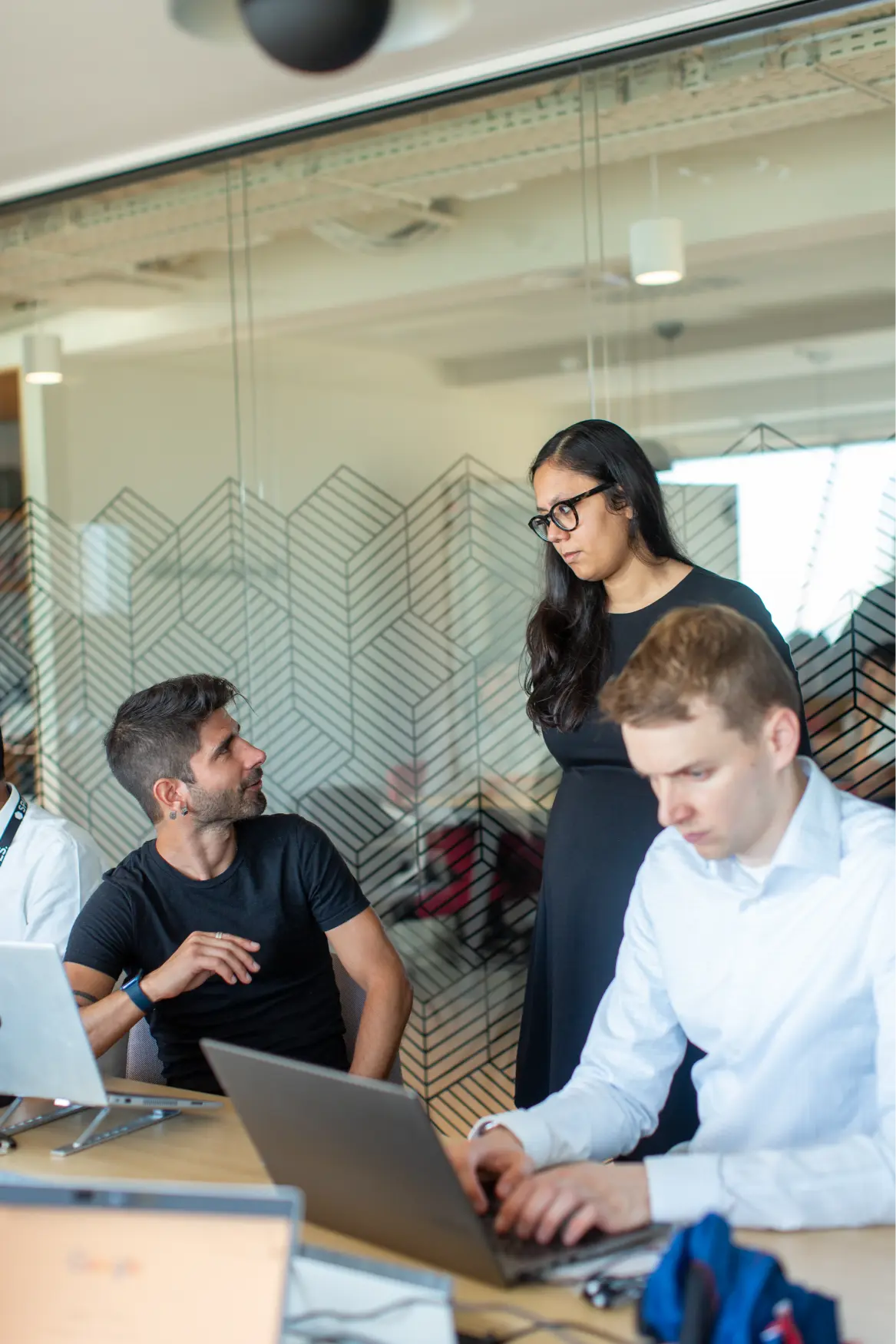
Unlocking innovation beyond IT
The Splunk platform lets Siemens DI and its business users see directly into their data, and spot and efficiently resolve data issues, reducing costly delays. But that’s just the beginning. “The next logical step would be looking into content, looking into real data,” says Hecht. “Not so much for the IT teams running those platforms, but it’s for the business users who can get insights into the data. Using Splunk, we could run any kind of relevant analysis on that content in the data store that is useful for our business partners.”
With Splunk and Rojo, Siemens DI could allow users to reprocess failures with the click of a button and offer consumption-based pricing. “We can build integration for our customers, but now we can show them the higher-value processes that Splunk makes possible,” says Hecht.
"If errors come through [during ETL-based processes], it can be difficult to know where they’re coming from. Splunk gives everyone the ability to quickly find the problem and resolve it." - Thomas Hecht, IT Project Lead & Corporate Process Owner for Product Master Data, Siemens Digital Industries